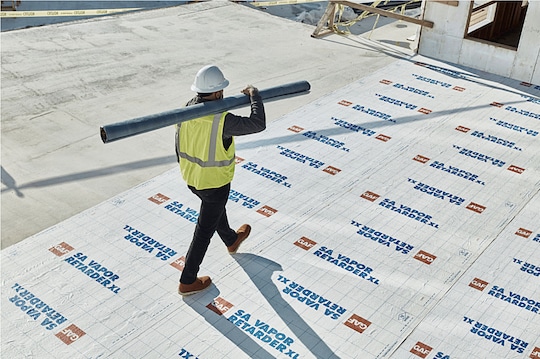
Is thermal mass a lost art form after centuries of use in temperate regions?
In building design, the thermal mass of a building enables it to store heat, providing "inertia" against temperature fluctuations. It reduces the impact of external daily temperature swings on internal heating and cooling requirements. This thermal inertia has been an on-off again topic of discussion for some time. Proponents of adding thermal inertia point to Mediterranean area buildings constructed with thick stone walls and ceramic tile floors etc. Such buildings have kept occupants cooler than lighter weight buildings in many temperate areas of the world for centuries. In the quest to improve the energy efficiency of buildings, further gains are becoming increasingly harder to come by.
- Code requirements for increased thermal insulation in the US have reached the point of rapidly diminishing rates of return.
- The use of highly reflective roof membranes has become widespread, with white or light-colored thermoplastic single-ply now representing over 60% of roof coverings installed each year.
- Airtightness of buildings, achieved with an air barrier around the entire building envelope, has been improved significantly over the past decade and further improvements will be increasingly harder to obtain.
This article explores how the thermal inertia of low-slope roofs can be a factor in improving thermal efficiency when considering building geometry, climate, and use.
Introduction
It is helpful to review the role of each part of a roof assembly in terms of its effect on energy efficiency, beginning at the top portion that directly faces the sun and sky. There are two main effects that building envelope materials have on thermal energy (i.e. heat) transmission that are explored here.
- Thermal resistance, which is a measure of the extent to which a material blocks or resists heat transfer. Building designers and construction professionals are very familiar with this and R-value, a numerical description of the extent to which a material can resist heat flow.
- Time delay of heat transfer, or the extent to which a material slows down or delays heat transfer. As will be seen, a material can have low thermal resistance but still delay heat transfer. This is the crux of the terms "thermal mass" and "thermal inertia".
Solar Heat Energy Impacting Roof Surface
It should be fairly clear that the peak of the sun's heat impact on a roof is around 1pm, and has lower impact in the early morning and late evening hours. This is shown in the following schematic:
- The amount of the sun's energy reaching the roof shown above peaks at around 1pm. For this reason, power output from solar panels is maximized at that time.
- Rooftop surface temperatures are at their highest at around 1pm.
- The amount of solar energy at midday in June, when the sun is at its' highest, is about 1 kW/m2 in the southern US. This is considerable and is why energy efficiency efforts focused on air conditioning demand are so important.
Impact of Reflective Membranes
Highly reflective roof membranes such as TPO and PVC are capable of reflecting well over 60% of the sun's energy (see CRRC rated products directory for actual values). For a roof with zero insulation, this would have the effect of reducing the amount of solar heat energy moving through the roof into the building, as shown here:
- The energy entering the building is reduced because some is reflected off the roof surface by a reflective membrane such as TPO or PVC.
- The peak energy flow through a membrane coincides with the sun's highest point, around 1pm.
Impact of Reflective Membranes and Insulation
When insulation such as polyiso is installed beneath a highly reflective membrane, it further reduces the amount of solar energy entering a building, as shown below:
- The heat energy entering the building is further reduced by the insulation.
- Importantly, there is a small time delay and the peak energy flow into the building is after the sun has already passed its highest point in the sky.
Building codes have steadily increased the amount of insulation required. However, each additional unit of insulation added is less effective than the previous units. This is shown in the following chart:
- Further gains in energy efficiency through the use of more roof insulation are becoming less and less cost-effective due to the law of diminishing returns.
- Greater thicknesses of insulation cause difficulties with respect to perimeter, parapet wall, and penetration heights. Insulation technologies with greater resistance per inch of thickness, like aerogels and vacuum insulated panels, have not yet proven to be widely cost-effective in roofing applications.
- Energy efficiency improvement efforts have recently focused on creating an air barrier around the entire building enclosure in large part due to the limitations in adding more and more insulation. By having the building enclosure perform as an air barrier, conditioned air is retained within the structure.
- Most considerations of a roof assembly primarily consider membrane, insulation and, when used, cover boards. However, given that cover boards are typically thin and therefore of low mass, it is the roof deck that offers the best chance of increasing thermal inertia.
Impact of Roof Deck
The roof deck is frequently taken for granted and not discussed as part of the roof assembly. However, it can make a contribution to energy-efficiency as discussed here. The following schematic shows two very similar roof assemblies. However, the left-hand design is on a steel deck while the right-hand system is over a concrete deck.
- Both systems have two layers of polyiso with staggered and offset joints to reduce heat flow.
- The steel deck system above has a mechanically attached first layer of polyiso. By minimizing the thickness of this first layer, the fasteners can be buried within the system to reduce thermal bridging.
Due to its metallic nature and relative thinness, the steel deck has essentially no effect on energy efficiency.
- A roof assembly on a steel deck will generally have the same heat flux into the building as shown above for the membrane and insulation only.
- The thin steel deck doesn't absorb any significant amount of heat and it has almost zero thermal resistance.
A concrete deck has what is known as "thermal mass", providing inertia to any heat flow. This results in a slowing of the heat flux into a building as shown below:
- A concrete deck significantly slows the transmission of heat down into a building but it doesn't necessarily have a high thermal resistance (lightweight insulating concrete is a special case and will be covered in a future article).
- During multi-day cycles, thermal inertia tends to dampen out temperature swings as shown in the following chart:
- By dampening out temperature swings, thermal inertia can increase thermal comfort within a building enclosure. If this effect is coordinated with the mechanical designer it can also help reduce upfront HVAC equipment sizing and costs that would have otherwise been designed to offset higher peak energy loads. (Of course, energy cost savings are not guaranteed and the amount of savings may vary based on climate zone, utility rates, radiative properties of roofing products, insulation levels, HVAC equipment efficiency and other factors.)
- Importantly, thermal inertia does not change the area under the heat flux curves. Looking at the plot above, the low points for a thermal mass assembly are higher than the assembly without thermal mass.
Thermal Inertia and Energy Efficiency
As noted in the beginning, thermal inertia has been incorporated in Mediterranean building practice and has kept buildings cool during summer periods. However, a close analysis reveals that while temperature swings are reduced and thermal comfort increased, energy-efficiency of air-conditioned buildings aren't necessarily improved.
There have been many published modeling exercises that have examined the long term energy-efficiency of building enclosures that incorporate significant amounts of thermal inertia
- All studies show that materials with high thermal inertia are best installed on the inner side of a building enclosure and insulation on the outer side. So, low slope roof assemblies with the membrane at the top, over insulation, and a concrete deck at the bottom, would meet this.
- While many studies claim to show improvements in building energy-efficiency when thermal inertia of the building envelope is increased, there are as many studies showing that there is no long-term effect
- A comprehensive review of published studies has suggested that the large differences in outcomes are a result of differences in assumed building usage, thermostat controls and settings, climate, and building geometry and location.
Examination of many peer-reviewed studies suggests the following:
- Thermal inertia has a small or insignificant effect on heating efficiency.
- For buildings occupied around the clock, thermal inertia is unlikely to affect overall energy-efficiency regardless of climate. However, it may improve thermal comfort by reducing the magnitude of thermal swings.
- For buildings that are only occupied during daylight hours, such as office buildings, increasing thermal inertia could move peak cooling demand into late afternoon and evening hours.
- If setback thermostats were employed, this could result in a reduction in cooling costs and an improvement in thermal comfort.
- In larger buildings with variable speed HVAC fans, the system could drop to a lower speed during evening hours, thereby lowering energy use.
- For thermal inertia to be an important factor in roofing design, such as for office buildings which are only used during daylight hours, the roof area would have to be a significant part of the building enclosure. In other words, the use of thermal inertia to lower energy use would be more appropriate for low rise buildings.
Characterizing the Effects of Thermal Inertia
There are two key characteristics of thermal inertia; the decrement factor and time delay, both of which can be readily modeled and experimentally verified. A schematic showing these is shown below:
The time delay is calculated as:
- The time delay and decrement factor could be used by building designers to better optimize thermostat specification. As noted earlier, a large time delay could significantly reduce daily AC cooling demands and peak loads for office buildings.
- Larger decrement factors can improve occupants' thermal comfort.
Conclusions
- Increasing the thermal inertia of roofing systems could be beneficial in regions where air conditioning dominates versus heating.
- Thermal inertia can be increased by using concrete decks. In fact, modeling suggests that when adding thermal mass to a building enclosure ensuring the mass is on the interior and continuous insulation is to the outside is the only way to potentially improve energy-efficiency. A design professional should be consulted to determine whether a concrete deck is appropriate on a given project.
- On a longer-term basis (over 48 hour periods) for buildings used 24 hours a day, increasing thermal inertia is unlikely to improve energy-efficiency. Increased thermal inertia dampens temperature swings and peak demand loads, but the overall heat flux isn't reduced significantly.
- Adding thermal mass could be advantageous for buildings occupied during daylight hours only. These would include schools and office buildings for example. By delaying heat flux down into those buildings, energy usage could be reduced so long as set-back thermostat control or similar ways to reduce energy usage during unoccupied hours are used. These could include reducing variable speed HVAC fans to a slower set point during evening hours. A design professional should be consulted to determine appropriate ways to add thermal mass on a given project.
Note – diagrams and charts shown in this article are not to scale and are for illustration of key points only.
Sources Used
- Verbeke, S., Thermal inertia in dwellings. Quantifying the relative effects of building thermal mass on energy use and overheating risk in a temperate climate. PhD Thesis, University of Antwerp, 2017.
- Balaji, N. C., Mani, M., and Venkatarama, R. B. V., Thermal performance of building walls. 1st IBPSA Italy Conference, Building Simulation, 2013, pp. 151 – 159.
- D'Orazio, M., Di Perna, C., and Di Giuseppe, E., A field study of thermal inertia of roofs and its influence on indoor comfort. J. Building Physics, 38, 2013, pp. 50 – 65.
- Kossecka, E. and Kosny, J., Influence of insulation configuration on heating and cooling loads in a continuously used building. Energy and Buildings, 34, 2002, pp. 321 – 331.
- Wang, D., Yu, W., Zhao, X., Dai, W., and Ruan, Y., The influence of thermal insulation position in building exterior walls on indoor thermal comfort and energy consumption of residential buildings in Chongqing. IOP Conf. Series: Earth and Environmental Science, 40, 2016