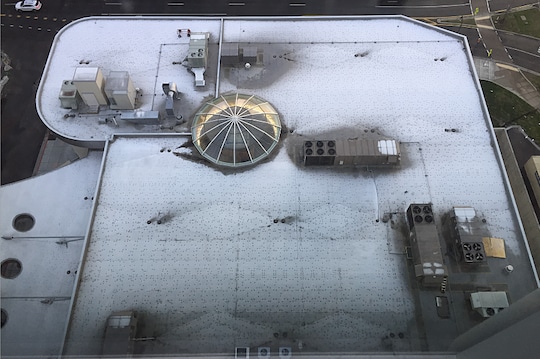
In the first Value Engineering post about the attributes of high performing roof designs, value engineering is defined as "a concept that states there are less expensive ways to get equivalent performance," and the post described the performance attributes that make for a long-lasting, high-performing roof system. These performance attributes include: images
- Energy efficiency (reflectivity, thermal resistance, and air leakage)
- Impact resistance
- Wind resistance
- Condensation prevention
- High heat (and UV) resistance
- Positive drainage
- Wear resistance
These performance attributes manifest themselves in certain aspects of the overall design of the roof system. What type of membrane, membrane thickness, cover board or no cover board, adhered or mechanically attached cover board, insulation layout (including tapered), insulation attachment method(s), vapor retarder / air barrier or not, and attachment to the roof deck are some of the questions that drive the performance of a roof system.
And the roof design is…
After considering all of the above performance attributes, your design strategies for a long-lasting, high performing, and durable roof include:
- Adhered reflective roof membrane with high heat-resistance
- Adhered HD polyiso coverboard
- 2+ layers of adhered insulation, staggered and offset, with tapered insulation and crickets and saddles
- Air barrier (over a substrate board) at the deck level
- Third-party-tested edge metal details
- Walkway pads
Energy Efficiency – reflectivity and thermal resistance
The attachment method is integral to a roof system's energy efficiency. Consider, for example, a roof that is designed to have the first layer of insulation fastened to the deck and the remainder of the components above are to be adhered. There is a cost for fasteners as well as adhesives. One way to "value engineer" this roof is to use fasteners through the entire system thereby removing the cost of the adhesive and labor to install the adhesive. While eliminating the adhesive is a cost reduction strategy, it is possible that longer fasteners will be needed. Sometimes something that is eliminated creates the need for a greater cost elsewhere. This is often not mentioned or discussed, so ask the question!
Value engineering the removal of the adhesive also, unfortunately, can result in a roof system with a 15 to 30% reduction in R-Value relative to the as-designed roof system. If the roof was designed to have an R-30, the actual R-value as installed would be about R-21 to R-25! It's been shown that over the life of a roof, roof systems that use adhered membranes and an adhered top layer of insulation can offset the cost of adhesives when the initial cost of 'lost' insulation performance and the additional annual cost for increased heating and cooling are factored into the analysis.
One of the key issues with value engineering of a roof system is that proponents of the reduction of costs are generally only looking at the initial cost to install a roof. However, the operational costs, the energy efficiency, the wind resistance, are commonly compromised. Operational costs, which are tied directly to a roof system's energy efficiency, are often much higher over the life of a roof. Also, roof systems with different wind-resistance ratings may need to be selected after value engineering revises the attachment method.
Also, is the mechanical system design and whole-building energy-use analysis predicated on a roof system R-value of 30? Determining the effect on mechanical unit sizing and cost, including differences in whole building energy use may show that the savings from value engineering the roof will have a negative effect on annualized energy use and the ability of the HVAC system to maintain occupant comfort. Whole building energy simulation modeling, such as EnergyPlus™ (EnergyPlus.net), can be used. EnergyPlus™ is funded by the U.S. Department of Energy's Building Technologies Office, and managed by the National Renewable Energy Laboratory.
Each "dot" is a fastener and plate; fasteners and plates are thermal bridges that reduce the R-value of the insulation layer.
Impact Resistance
Using any type of coverboard will improve the impact-resistance of a roof system because of the toughness of coverboards in general. However, a key issue with impact resistance is the location of the plate and fastener relative to the roof membrane. If a coverboard is mechanically attached (so the plates and fastener head are immediately beneath the membrane), impacts at fastener heads and plates have been shown to result in damage to the membrane. Adhered coverboards remove this concern, but do require the use of some type of adhesive. It's not just the use of a coverboard, but the installation method that matters.
Ice-ball impact above fasteners always punctures the membrane. Left to right: increasing damage from hairline crack to complete puncture.
Impacts come from hail as well as rooftop use by occupants and anyone performing work on rooftop mechanical units or to rising walls, for example. Reducing membrane thickness, changing from a fleece-back membrane to a smooth-back membrane, as well as changing to a more commodity-type membrane versus one that is shown to have a long service life are value engineering choices that can reduce cost, yet also reduce the impact resistance.
Wind Resistance
Designers make wind-design decisions that are intended to reduce risk (e.g., choosing Partially Enclosed versus Enclosed, selecting Exposure Category C instead of Exposure Category B). If a designer and owner have determined to reduce the potential risk of high-wind-event damage by increasing the design wind loads and subsequently the capacity of a roof system, that high capacity could be value engineered out. Coordinating wind design assumptions and documenting owner expectations and decisions can be critical pieces of information that alleviate the reduction of wind load capacity based on cost. Owners have their reasons; value engineering should not undermine owner expectations. By including design wind pressures for each roof zone as well as providing design loads for edge metal, and parapets and coping, minimum performance requirements are established in the construction documents.
For more on wind design, read our blog here.
Condensation prevention
Roofs that include air barriers above the deck and below insulation provide the best protection against the development of condensation in a roof system. Your roof design took into consideration the interior and exterior design temperatures and calculations were performed to determine potential dew point locations, which resulted in the correct placement of the air barrier.
This roof design is "above code." While the energy code allows the roof membrane to be the air barrier, air can still move up into the roof system. This is called air intrusion and can bring moisture into the roof system, potentially causing condensation issues.
Placing the air barrier layer on the top surface of a rigid board fastened to the roof deck is one option. However, with "first layer fastened and the upper layers (insulation, cover board, membrane) adhered" systems, there is an opportunity to include a vapor retarder / air barrier between the insulation layers without fasteners penetrating the vapor / air barrier layer. Reducing air intrusion and the potential for condensation is achieved using both designs; this is a real value engineering opportunity! The costs for materials and labor for each design can be determined, and the least expensive design that provides condensation control can be implemented, instead of eliminating the properly located air barrier.
While removing the air barrier and the associated adhesives and components reduces costs, changing to a roof system that uses only mechanical attachment also negatively affects the potential for condensation and thermal performance of the roof system. For example, consider a high-humidity building, such as a natatorium—the use of an air barrier at the deck level reduces air intrusion into the roof system from the interior and the moisture that air carries. This reduces the potential for condensation and damage to the roof system.
High Heat (and UV) Resistance
Heat and UV are two environmental factors that affect roof membrane service life. Understanding this and that storms are increasing in severity and frequency, in addition to recognizing temperatures are rising (ASHRAE's climate zone maps are moving northward), your roof design includes a membrane that has been shown to have a long service life. It's likely the specification includes GAF's TPO Everguard Extreme® membrane due to its ability to withstand high heat conditions.
It's possible that a high-performing roof membrane will be value engineered down to one of reduced initial cost. The rationale will be that it still keeps water out! But to what long-term cost? You designed a roof to meet your client's expectations for a long service life. By considering annualized costs, not simply initial cost, it may be shown that a longer service life roof is actually a better long-term value for the owner. A key strategy is to use annualized costs when pushing back against value engineering.
Positive Drainage
Most roof systems are not guaranteed or warranted against ponding water. The combination of UV and water is one mechanism that advances the deterioration of many roof membrane materials. And because water needs to be removed from a roof quickly and efficiently, your roof design includes properly sized drains and scuppers, a tapered insulation layout to efficiently move water to drains and scuppers, and crickets and saddles to prevent localized ponding.
Example of a tapered layout, courtesy GAF Tapered Design Group
When asked to reduce the cost of the tapered insulation, one possible answer is to install more drains that are closer together. This can reduce the build-up of tapered insulation, and the associated cost. Perhaps the use of lightweight insulating concrete is less costly? Perhaps the use of a TPO membrane, which does not have ponding water limitations in the guarantee/warranty, makes sense?
Wear Resistance
Thicker membranes, granulated surfaces, and walkway pads are helpful in preventing unwanted wear to roofing membranes. You've coordinated expectations with the owner, your client, that rooftop protection against wear and tear is important during the operation phase of the building. Reducing the thickness of a membrane reduces its potential wear resistance, as well as its impact resistance (as previously noted in this blog). As with many things, none of these issues are stand-alone issues.
Perform a cost comparison of a granule-surface modified bitumen membrane and a smooth surface system with a high-solids coating system to see if there are less expensive systems that still meet wear-resistance requirements. Don't just look at initial costs; consider maintenance costs over the life of the roof that affect annualized costs. A relatively small number of walkway pads, strategically placed around rooftop units and systems that will require regular maintenance (e.g., HVAC units and solar arrays), can be an effective and economic solution.
Product substitutions
Not all products with the same intended function (and described with the same terminology) are created equal. A vapor retarder is a good example. A self-adhered vapor retarder with a perm rating of 0.03 has a desired performance and was included for a specific reason – to effectively block the diffusion of moisture into the roof assembly. Substituting a less expensive vapor retarder with different properties (e.g., a higher perm rating) and physical characteristics (30 mil asphaltic vs. a 6 mil poly), won't be installed in the same fashion—even though they are both vapor retarders. The least expensive material may be the most costly to install properly.
Details
Details matter. Without a doubt, the ability for a roof to keep water out is most challenging at the details—penetrations, perimeters, and locations where there is an interruption, end, or change of direction. You designed a two-part counterflashing for ease of maintenance and future reroofing; a single-piece counterflashing is less expensive initially. When it's time to reroof, will the facade material (e.g., masonry, stucco, EIFS) need to be removed and repaired in order to install new counterflashing? Again, you've established with the owner that future efforts for maintenance and reroofing are important.
There are ways to value engineer roofing details, especially when it comes to air barrier and vapor retarder constructability. A good example is an overhang. It seems logical to design an air barrier to enclose the overhang (the blue lines in the graphic), but there are many potential dis-continuities (the red lines in the graphic). The air barrier can be inboard of the eave; the wall air barrier could be tied to the underside of the roof deck, and the above deck air barrier (whether at deck level or the roof membrane) is tied to the top of the roof deck making a continuous air barrier system. There likely are labor savings associated with this value-engineered design revision.
Weather
A change of seasons is often the impetus for changing from an adhered system to one that strictly uses mechanical attachment. While this may not be value engineering, a change of seasons can mean daily temperatures are below manufacturer recommended minimums for adhesive materials. However, manufacturers have (and are developing) lower temperature adhesives. Regardless of why a roof system design eliminates adhesives in favor of fasteners, there are energy efficiency and an impact-resistance trade offs.
Owner expectations
Much of the prevention of value engineering is having a clear understanding of the owner's performance requirements and expectations. Getting 'buy-in' from an owner for high-performance roof systems is key. During the design phase, explaining the importance of design decisions and aligning them with the owner's performance requirements should be documented. Documented design decisions that are made in conjunction with the owner provide a defense when "it costs too much" is used as the basis for value engineering.
The Whole Building Design Guide, from the National Institute of Building Sciences, includes detailed information about value engineering during the design and construction phases of a project.