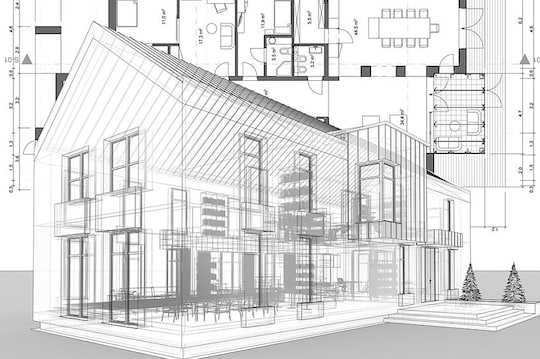
Wondering what roof decking is and what it's used for? Just as the foundation is the load-bearing portion of your home, decking is the load-bearing portion of your roof system. When a new home is built, flat and sturdy decking is installed between roof rafters and trusses. Then, roofers secure the roofing components that protect your home from the weather (like leak barriers and shingles) on top of that decking.
Is It Decking or Sheathing?
Roof decking and roof sheathing are two names for the same thing. Decking materials can include plywood, oriented strand board (OSB), wood planks, tongue-and-groove boards, and metal. Plywood and OSB are both common choices for builders and homeowners because of their flexibility, strength, and relative affordability. Decking is designed to be strong and resilient so it can bear the load of your roofing system, as well as other weight, such as snow.
Where Is the Roof Decking?
Your decking isn't visible from outside your house because it's underneath the roofing components. It is the dividing layer between the inside and outside of your home. After a wooden frame is built and the decking is placed, the roofing system is installed on top. Each part of the roofing system is layered on top of the previous one. Here are the components that make up a GAF roofing system in the order they are installed:
- Leak barrier
- Roof deck protection (underlayment)
- Starter strip shingles
- Shingles
- Ventilation
- Hip and ridge cap shingles
When Should I Replace My Roof Decking?
Replacing decking depends on the integrity of the decking system itself. Remember, decking is the structural basis for your entire roof system. That's why it's important to replace decking in cases of moisture damage, rot, holes or cracks, shrinkage, warping, or other decking inconsistencies.
Does a New Roof Mean New Decking?
Repairing or replacing a roof does not automatically mean you need new decking. However, a repair or new roof installation is a great opportunity to inspect the decking and verify it's in excellent condition. You want your entire roof system to weather the upcoming years with strength.
If your decking has water damage or other integrity issues, it can't serve as a secure basis to uphold the components of the roofing system.
For example, damaged decking might not securely hold shingle nails. Loose shingle nails result in loose shingles. Loose shingles can lead to leaks, shingle blow-off, and eventually structural damage to your home due to moisture infiltration. Appropriate decking is so important that international residential codes, most local building codes, and most roofing manufacturer requirements insist on a solid sheathing prior to shingle installation.
How Can I Tell If I Have Damaged Roof Decking?
As a homeowner, you can visually inspect your roof on a semi-annual basis or after significant weather to check for possible decking issues. Signs that can indicate damage include:
- Dips or swells in the roof surface
- Interior moisture damage
- Visible holes in the roof due to impact or weather
- Mold on ceilings or in attic rafters or decking
- Dry rot, especially near the roofline or in the attic
- Moisture or mold in the attic insulation
What Should I Do When Reroofing?
Sometimes when you reroof, you need to repair or replace your decking. Roofers can't always predict this need ahead of time because the decking isn't always visible from the exterior. For example, if moisture has seeped through loose shingles and weakened the decking, your roofer will need to resolve the problem before installing the new roofing components over the top. Otherwise, installing a new roof over damaged decking would mean that your roof's defense system has a weak link. In cases where repair or replacement of decking is required, your roofers may have to amend their initial quote.
What Do I Ask the Contractor?
In case your roofer tells you that you have damaged decking, it can be helpful to understand more about how the damage occurred and what it means moving forward. You can ask some of these questions to empower yourself:
- What is the damage and how was it caused?
- Has there been damage to other parts of my home as a result of the decking issues?
- What material will you use to replace my current decking?
- What are the pros and cons of the material you're recommending?
- Do I need attic ventilation? If so, what will you use?
- How will the decking repair or replacement impact my quote?
Remember, decking will help uphold your roof for decades to come, so it's important for it to be a solid foundation. If you are concerned about your roof decking or want to get started on a new roofing project, contact a contractor certified by GAF* today.
*Contractors enrolled in GAF certification programs are not employees or agents of GAF, and GAF does not control or otherwise supervise these independent businesses. Contractors may receive benefits, such as loyalty rewards points and discounts on marketing tools from GAF for participating in the program and offering GAF enhanced warranties, which require the use of a minimum amount of GAF products.