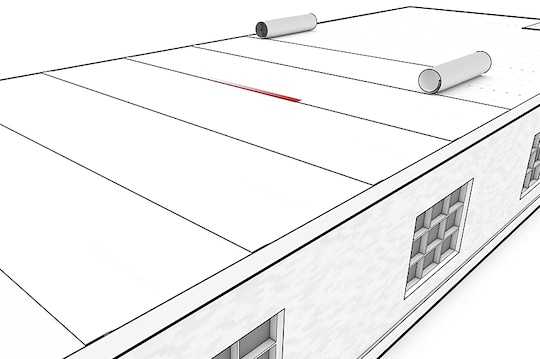
Working with the GAF Tapered Design Group, GAF Senior Commercial Training Specialists Dave Scott and Wally Brown (Dave & Wally) evaluate a plan for optimizing roof drainage using tapered ISO insulation. Mira cómo todo se combina en la parte 4 de la miniserie Roofing it Right sobre la instalación de un techo comercial, de principio a fin.
Watch the full Roof Project from Start to Finish miniseries.