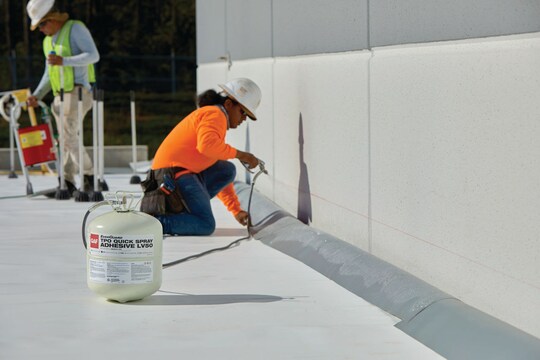
Como contratista de techado, sabes lo ruidosos que pueden ser los proyectos de techado. And when repairing or replacing roofs on institutional properties, like schools and healthcare centers, it's often not possible to remove occupants during the project's duration.
Accordingly, minimizing disruption at these facilities is key, as students need to be able to concentrate and patients must be protected as they recover. Here are common disruptions to consider and how to reduce them, with insight from GAF Building and Roofing Science Research Lead, Elizabeth Grant.
Common Disruptions on Construction Sites
You have several challenges to consider when working on schools or other facilities with ongoing operations, including noise, odors, and occupants' safety.
Elevated Volume
Heightened noise levels can affect both students and patients. En las escuelas, los sonidos fuertes pueden afectar la capacidad de los estudiantes de aprender y concentrarse. Likewise, construction noise can impact patients' ability to rest and recuperate in healthcare facilities.
Strong Odors
When using certain roofing materials on big job sites-like powerful adhesives or hot-mopped roofing systems-odors may infiltrate the building. This may be distracting and affect the comfort of students and patients.
Heavy Machinery
Unloading and staging material can also cause disruption, as materials must be staged onsite to be ready for installation as the job progresses. A menudo, esto involucra usar equipos pesados, como grúas y elevadores. Proper safety protections must be in place to ensure worker and occupant safety.
Roofing Products That Minimize Disruption
Unfortunately, there's no good time for a roof repair or replacement at a medical facility. You may be able to complete school projects when school is out of session, but that isn't always the case if a leak or storm damage occurs.
The best (and most proactive) way to minimize disruption is to use durable, long-lasting materials, as this reduces the number of times crews need to work on the roof.
Membranas TPO (Thermoplastic Polyolefin) membrane-una sola capa
Grant recommends a robust single-ply membrane or a system with some redundancy, such as a multi-ply modified bitumen. She also suggests leveraging a hybrid system, composed of a multi-ply modified bitumen system with a single-ply top sheet for reflectivity.
Cover and Substrate Boards
For resiliency against noise-causing conditions such as hail and foot traffic, Grant suggests using cover and substrate boards. Cover boards are installed on top of the insulation and provide sound insulation, while substrate boards are installed directly on the roof deck under the insulation.
"If you have a really noisy location, and you want to keep people inside from hearing a lot of disruption, having cover and substrate boards included in the system can be really important," says Grant.
Adhesives and Fasteners
Another change you can make to reduce disruption is using adhesive to attach roofing products instead of mechanically fastening them. This helps avoid the noise from driving fasteners into the roof deck-and enables a faster installation.
Grant notes that, depending on the FM and wind ratings required, it may be possible to adhere all the system components, including the insulation, cover boards, and membrane. An adhesive like GAF EverGuard® TPO Quick-Spray Adhesive can effectively adhere TPO and PVC roofing materials. El producto cuenta con una alta pegajosidad inicial, lo que posibilita una instalación más rápida que los adhesivos tradicionales. You can also opt for self-adhering products (vapor retarder, pipe boots, TPO roofing, etc.), which can further reduce installation time by eliminating adhesive application from the process.
Materials That Shorten Project Timelines
A creative and efficient way to minimize disruption at school and hospital job sites is to reduce the time crews are on the roof. By taking advantage of time-saving materials, you can reduce the risk to workers and occupants, increase productivity, and ultimately take on more work.
In addition to the Quick-Spray Adhesive, GAF offers several materials designed to cut installation time and labor:
- Wider rolls of TPO (12 feet instead of 10 feet) can help crews to spend less time installing systems on wide-open roofs.
- Insulation installation is easier with lightweight Ultra HD Composite Insulation, and it eliminates the need for one full application of adhesive in adhered systems.
- TPO self-adhered membrane can cut installation time by as much as 60% compared to installation using traditional bucket and roller adhesives.
Experienced Support That Streamlines Work
In addition to product and material selection, you can minimize disruptions by having GAF professionals from the Tapered Design Group help design the tapered insulation system. These professionals can help you with a variety of services, such as:
- Diseño de aislante biselado
- Tapered insulation Inventory management and ordering
- Budget friendly alternatives
Tapered insulation systems are designed to improve the drainage slope on roofs with substrate damage or without enough slope. El equipo de diseño biselado de GAF "equilibra una pendiente adecuada con la menor cantidad de material", explica Grant. "To help with saving money, saving material, and saving time."
This group designs tapered insulation systems that can be loaded and labeled strategically to minimize material handling and time spent looking for and transporting materials. Los productos se agrupan por área del techo, y un plan codificado por colores distingue las áreas para cada paquete. Materials are precut and specifically designed for each project.
Additional Tools to Save Time and Labor
Another GAF tool can help you reduce the time spent on projects: GAF QuickMeasure™ Reports.
GAF QuickMeasure™
GAF QuickMeasure™ provides complete roof measurements including parapet wall lengths, heights and widths to help create estimates, past views showing how a roof may have changed over time, grid-lined paper for buildings with a predominate pitch of 0 or 1, and a DXF file output for CAD.
There is also the ability to add on local design criteria and hail and wind history to help inform design decisions.
With the help of GAF QuickMeasure™ and the Tapered Design Group, you can confidently give your healthcare clients and school customers accurate estimates for suitable roofing products to meet their needs. These tools can also minimize disruption to building occupants and help building owners select durable, long-lasting products that will protect their investments for years to come.
Leveraging GAF Professionals' Experience
When working on schools, hospitals, and other important institutions, you're working to satisfy not only your clients but the individuals visiting these locations. By minimizing disruption, you can help ensure everyone involved experiences minimal disruption while you complete the project.
For more insight into time- and labor-saving products and services, explore GAF School Rooftop Resources.