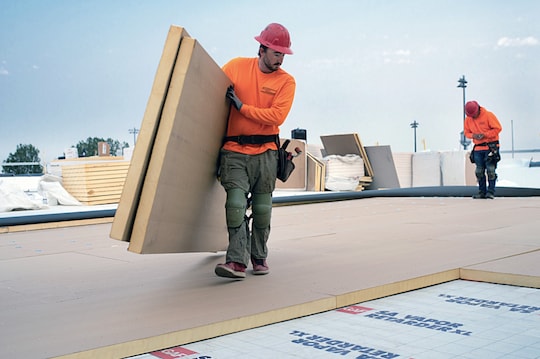
This post is part 3 of 3 on wind design. In part one, The Details Make the Difference in Wind Design, we discussed the importance of using tested edge details, such as those listed in ANSI/SPRI/FM 4435/ES 1-11.
One example used was NRCA TP-3 (above), which consists of the roof membrane running over the roof edge, the TPO coated metal being fastened on top with a cleat along the bottom edge, and then a strip of TPO hot air welded to the top of both the metal and the roof field membrane to complete a weather-tight seal. This detail also has the addition of bonding adhesive between the membrane and wood nailer, and sealant between the membrane and metal. The next detail, 202A from the GAF manual (right), is very similar to the NRCA detail, since both have the field sheet turned down the face of the wall with the metal edge over the field sheet, stripped into the field sheet, except it does not contain the bonding adhesive or sealant. In contrast, one commonly value-engineered detail (simulated below) consists of hot air welding the field membrane directly to the top of the TPO coated metal. The basic difference between the GAF and NRCA details, on the one hand, and the value-engineered detail, on the other hand, is a few more inches of field membrane, the addition of the TPO strip and one extra hot air weld along the length of that detail on the perimeter.
The benefit of the industry-recommended details (NRCA TP-3 and GAF 202A) is the use of the TPO coated metal as protection for the roof membrane. The industry-recommended details also provide two layers of weather protection-the field membrane and metal edge-for this critical location, and provide greater ability to allow expansion and contraction of the edge metal without jeopardizing the integrity of the connection. Importantly, installing the field sheet down the face of the wall provides a secondary layer of protection under every joint in the metal edge, which means two layers are helping to keep water out of the building, not one as is the case in detail 3.
In the scope of the entire project, these are examples of minimal cost addition with major performance enhancement. In the first 2 blogs, we discussed the importance of edge details and their role in wind uplift resistance, and the differences in determining wind loads based upon location, method, and how conservative you would like to be. These are great in theory, but when it comes to the person paying for the building, the real question is what is an "appropriate and conservative" design going to cost me?
What is an 'appropriate and conservative' design going to cost me?
Perhaps a good follow up question would be, "How well do you want to sleep at night?" While it is not possible to give actual monetary values, we can discuss the difference in assemblies and their subsequent components to help understand what those differences actually mean in terms of performance versus relative cost. In some cases, the additional protection may take the form of an additional step. In other cases, an entirely different systemic approach may be preferable. Here, we shed light on some of these factors to assist the design community in making educated decisions.
While it is highly recommended to use ANSI/SPRI/FM 4435/ES 1-11 tested details (1&2, not 3), any other potential options can be added to the construction documents as an alternate bid item, so the designer and owner can more easily have the actual cost versus resilience discussion.
A common mistake is to look at the cost of a component alone without comparing the labor cost.
One important thing to consider is that any system or detail has two costs associated with it: labor and materials. Labor cost is typically more than material cost and can be the hardest to manage. With materials, linear footage and/or "area plus waste" is relatively simple to calculate and control. However, labor costs may be impacted by many different factors, including weather and environment, site specific issues, safety procedures and equipment, and the cost of items such as employee benefits, which exist on top of the hourly cost. Designers and owners will typically benefit from details that weigh more heavily on the cost of materials to compensate for additional labor, both in the overall cost and schedule impact. A common mistake is to look at the cost of a component alone without comparing the labor cost. One example of this is the use of pre-manufactured components as opposed to fabricate-in-place components. Another good example is upgrading from a 45-mil thick membrane to 60-mil thick membrane. There are small material cost increases, with virtually no accompanying labor cost increases, that may greatly enhance longevity and performance.
Now, with that being said, consider the detail to the right. This is a pre-manufactured edge-metal system. An aluminum cleat is attached over the field membrane that turns down the face of the wall. The edge metal system is attached into the face of the nailer (not the top). Then the fascia metal, with a choice of a few dozen colors, is snapped into place. There are a lot of benefits to this detail: the designer can choose color; there is no stripping in or welding on the roof edge; installation allows for thermal expansion and contraction; and this is an ANSI/SPRI/FM 4435/ES 1-11 tested detail that may be eligible for extended warranty or guarantee protection (up to 35 years) with the appropriate system. This easy-to-install, pre-manufactured edge metal system provides weather protection that is comparable to a multi-step, contractor-fabricated edge metal system. While the material cost may be more, the reduction in labor costs will often result in this detail being more cost-effective overall.
Switching gears
When it comes to a roof system's uplift resistance, things can change more drastically. In general, a fully adhered roof will resist higher uplift pressures, followed by an induction welded system (commonly known as Rhinobond, a trade name of OMG), followed by a mechanically attached roof system. But at what cost? In most cases the cost of adhesive, and the fact that each layer of material must be adhered, makes a fully adhered roof the most expensive system. A 500 square roof with 4 layers of roofing components (e.g., 2 layers of thermal insulation, a cover board, and a membrane) requires 2,000 squares worth of adhesive. A mechanically attached system is commonly believed to be the least expensive; however, a careful analysis of material usages shows the induction welded system to be less expensive on a wood or metal deck. The difference lies in the induction welded system requiring fewer seams than a mechanically attached system, no penetration of the membrane, and fewer total fasteners relative to a mechanically attached system. The induction welded installation results in significantly less labor and requires about 2.5% less membrane due to smaller overlap of seams (3" overlap as opposed to 6" overlap). From my experience, the relative cost difference holds true for roofs that are 200 squares or greater. The larger the roof, the greater the membrane and installation savings.
Of course, there are other concerns involved when selecting the appropriate roofing system. For example, moving from a fully adhered system to a mechanically attached system also has implications for the overall thermal resistance. Because fasteners through a roof system are thermal bridges that reduce the overall system R-value, increasing the insulation thickness should occur when going from an adhered to a mechanically attached system. Reducing the number of layers of board insulation from 2 to 1 also allows more air and water vapor movement into and through the system which increases the potential for condensation and related damage.
The real question to ask is this: What is the life cycle cost of your roofing choices?
There are trade-offs for almost all facets of a roofing system, from overall system design and attachment method to edge details. A building envelope design consultant can evaluate the end use of the building to determine the best overall roof system for a building. Factors such as numbers of occupants, activities and components that produce additional moisture, and the temperature and humidity as designed by the HVAC engineer are critical. Thermal bridging of fasteners resulting in reduced net R-value and mitigation of condensation potential are also potential pitfalls of choosing the less expensive roof.In some instances, minimal reductions of the initial cost of a roof system may have substantial long term performance reductions. The real question to ask is this: What is the life cycle cost of your roofing choices? The cheapest option initially may end up costing the same or even more than the higher cost options. The only real way to find out is to consult a building envelope design consultant to analyze the cost.
While roofing manufacturers will test systems for criteria like wind and fire resistance, they cannot predict the end use of the actual building envelope. This article is for general information purposes only - you should always consult with a building envelope design consultant to determine whether the roofing system to be installed is suitable for the particular needs of your building.