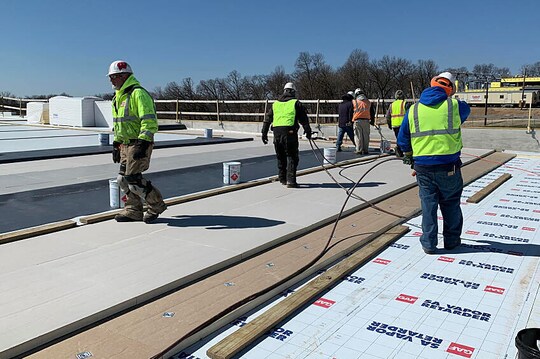
Ciencia de la construcción
Preguntas frecuentes sobre barreras de vapor
Cada vez más, se indica la inclusión de barreras de vapor en ensamblajes de techos con pendiente baja. Pueden ayudar a controlar el traspaso de aire húmedo del interior del edificio hasta la parte inferior de la membrana para techos. Además, ayudan a limitar la cantidad de humedad que traspasa de una plataforma base de concreto hasta la instalación del techo. De hecho, ofrecemos el retardador de vapor autoadhesivo (SA) GAF, una capa autoadhesiva, para ayudar a reducir el riesgo de que esto ocurra. If you are designing a new roof and want to reduce possible moisture risks or are replacing a roof assembly where there's evidence of moisture issues, this article may help you to understand more about the use of vapor retarders.In addition to this article, we also have a Guide to Vapor Retarder Design in Low-slope Roof Systems which describes best installation practices. El objetivo de la guía y de este artículo es abordar los aspectos básicos de las barreras de vapor para diseñadores que buscan solucionar los problemas de traspaso de humedad. Later articles will cover more fundamental considerations.The answers to these frequently asked questions may sometimes repeat key information, and the reader can jump to those questions of most interest. But reading all of the answers will help get a better overall understanding of the function and role of vapor retarders.What is a vapor retarder?It is a material that, depending on its exact specification and correct installation, blocks or slows down the transmission of moisture from one side to the other. Vapor retarders can be coatings, boards with taped joints, or membranes.Looking at this schematic, it is clear that in an actual roof assembly any penetrations have to be sealed otherwise the vapor retarder's function is degraded - more on this later.How does a vapor retarder function?A properly installed vapor retarder at the deck level can help slow down or block the movement of moisture from the building's interior migrating up into the roof roof assembly. Blocking or slowing down the movement of moisture can be part of an effort to lower condensation risks within the roof system during cold winter months.Vapor retarders can also have some degree of moisture permeability. Existen diferentes clases de materiales que retardan el vapor (I, II y III) y cada clase de material permite que diferentes niveles de vapor de humedad atraviesen los materiales mediante la difusión. La capacidad de limitar el movimiento del vapor y, al mismo tiempo, permitir que el vapor de humedad traspase el material puede ser importante, ya que puede evitar que la humedad quede atrapada dentro del sistema del techo. Roof membranes are moisture impermeable, so if moisture does get into the assembly, a properly specified vapor retarder with some degree of moisture permeability can allow the moisture to slowly escape downwards.How does a vapor retarder differ from an air barrier?To state the obvious, properly installed air barriers block air, and as a result will also block the movement of humid air, thereby retarding or stopping most moisture movement. Por lo tanto, pueden parecer muy similares e incluso idénticas. Sin embargo, el uso o la aplicación de cada una normalmente es diferente. For more on this, check out this article.A good roof membrane, such as GAF EverGuard TPO will not only block air and moisture but also withstand ordinary wear and tear.A good vapor retarder, such as GAF SA Vapor Retarder, is normally used within a roof assembly to reduce moisture movement. Tendrá una permeabilidad limitada o nula, ya que su objetivo principal es reducir el movimiento de humedad. While it can act as a temporary roof, it is not intended to be wear- and tear-resistant in the same way as a roof membrane.Is a vapor retarder required?Building codes do not require the installation of a vapor retarder in roof assemblies. Un diseñador profesional debe decidir si incluir una barrera de vapor. Otras respuestas de este artículo pueden dar una idea de lo que se podría considerar para esta decisión, pero un diseñador profesional debe ser quien tome la decisión final de acuerdo con las condiciones específicas del proyecto. Basically, a vapor retarder can be specified and correctly detailed in order to manage the migration of moisture vapor to prevent wetting and enable drying within a roof assembly.Does vapor retarder use depend on a building's location?The location has a significant impact on the decision to incorporate a vapor retarder into a roof assembly. El diseñador del edificio debe considerar la dirección principal del flujo de la humedad dentro del cerramiento del edificio. Keep in mind that moisture drive is normally from warm (high vapor pressure) to cold (low vapor pressure).If the building is located in the north, moisture drive is the strongest in the winter. El interior del edificio suele tener temperaturas más cálidas que el exterior. Todo el aire húmedo interior que llegue a las capas del cerramiento externo podría generar condensación debido a las temperaturas externas más bajas. In a roof assembly, a vapor retarder located towards the bottom side of the roof assembly can help reduce or throttle back the migration of water vapor from the interior warm side to the exterior cold top of the roof assembly.For a normal building occupancy and where the building is located in a consistently humid climate, the moisture drive is predominantly towards the interior of the building. En este caso, el aire húmedo caliente del exterior que penetre el cerramiento del edificio puede formar condensación en las superficies más frías del interior. Roof membranes are inherently vapor retarders so downward or inward vapor drive is blocked.For buildings with high occupant moisture generation, or that are located somewhere with a mixed vapor drive depending on the season, the roof designer should consider the appropriate roof assembly for the application. If moisture drive from the interior up into the roof assembly could lead to condensation within the roof assembly, then a vapor retarder should be considered.Isn't the roof membrane a vapor retarder? Why do I need another one?Roof membranes are generally vapor impermeable, but to be considered as vapor retarders one has to consider their use. En edificios en el norte con un flujo de vapor ascendente que penetra el sistema de techo, la membrana para techos actúa como barrera contra las condiciones climáticas del exterior. También se puede utilizar como barrera de aire para prevenir la filtración del aire acondicionado interior, pero no evita que el aire húmedo del interior se desplace hacia arriba y atraviese el sistema de techo. If water vapor is able to migrate upwards towards the roof membrane, then there can be a condensation risk depending on factors such as the exterior temperature and the interior humidity level.Where should a vapor retarder be placed within a roof assembly?The simplest answer to this question is as close to the interior conditioned space as is practically possible. Sin embargo, siempre se debe comprobar que los códigos contra incendios locales permitan la aplicación de membranas autoadhesivas directamente sobre las plataformas base de acero. En muchos casos, es necesario instalar primero un tablero de yeso o cemento sobre una plataforma base de acero, que luego se usará como sustrato para las barreras de vapor adheridas. Always check with the roof system designer to make sure that a proposed system meets all necessary codes.Alternatively, the vapor retarder could be applied to the topside of the first layer of insulation, but in such a case, the designer would need to confirm that the dew point would be above the vapor retarder.Can I use black poly (e.g. Visqueen) as a vapor retarder?Black poly sheet, technically 6 mil polyethylene, is often used as a vapor retarder in residential crawl spaces. However, its use in roof systems is generally not recommended for several reasons:It does not self-seal around fasteners that penetrate through it. Vapor retarders such as GAF SA Vapor Retarder are designed to meet a self-seal test described in ASTM D1970.Polyethylene is notoriously difficult to adhere to, which makes flashing and sealing around penetrations very difficult and unlikely to be durable.6 mil polyethylene is essentially impermeable, which means that any leak in the roof covering will let in water that can't escape. Además, si hubo agua presente cuando el techo estaba cerrado, proveniente del rocío o una lluvia ligera durante la noche anterior, no podrá escapar. Las barreras de vapor con las especificaciones correspondientes tienen cierto nivel de permeabilidad que permitirá el traspaso de agua desde el interior de un sistema de techo hacia abajo. The only exception to this may be for a building with a very high interior humidity when it might be advisable to have a vapor retarder with essentially no permeabilityMy building is in the north, so do I automatically need a vapor retarder?No, a roof designer needs to evaluate the risk of condensation occurring. El uso del edificio, el tipo de edificio y el diseño del sistema de techo son factores importantes. An evaluation of condensation risk asks questions including:What is the humidity level likely to be in the building? Office buildings can be expected to have lower levels versus buildings with restaurants or indoor pools.If activities within the building could generate high humidity levels, has the HVAC system been designed to reduce the levels with make-up air?What is the building's location and what are the coldest exterior temperatures that could be expected?Will the roof assembly inhibit air flow without the use of a vapor retarder? Some roof assemblies, particularly those that have adhered layers, are more restrictive of air flow than others.Once interior humidity levels have been estimated and outdoor cold temperatures known, then the building designer can calculate where the dew point will be in the roof assembly. If the designer specifies a vapor retarder, it should always be located below the dew point.How should a vapor retarder be tied in, flashed to penetrations, etc?To be successful, penetrations through the vapor retarder need to be flashed and air tight. Además, los bordes deben llegar a las paredes. Se debe tener cuidado para garantizar que el aire interior no pueda traspasar fácilmente la barrera de vapor y subir en dirección al sistema de techo o una pared del parapeto. The GAF Guide to Vapor Retarder Design in Low-slope Roof Systems provides system details to help guide good design.Should a vapor retarder be used with a concrete deck?In new construction, it can be difficult to ascertain when concrete decks are sufficiently dry to allow the roof assembly to be installed. If significant levels of moisture are present in the concrete deck after the roof is closed up, then problems can arise.For more on the topic of moisture in concrete roof decks see this article by my colleague James Kirby. Briefly, as advised by industry groups such as the Midwest Roofing Contractors Association (MRCA), the use of a vapor retarder over a concrete deck will limit moisture passing through to the roof assembly.In re-roofing situations over concrete decks, there is usually less concern about moisture being present within the concrete deck, providing that there have been no leaks. Sin embargo, si el techo originalmente se instaló con mínimo aislamiento, existe la posibilidad de que el concreto contenga suficientes niveles de humedad debido a la condensación, según las condiciones climáticas locales. Además, cualquier precipitación durante la renovación de techado podría propiciar la absorción de agua en la plataforma base de concreto. If there is any concern about moisture in an existing concrete deck, a vapor retarder should be considered.In new construction, is there a concern about moisture from a concrete floor or foundation?Yes, there can be, depending on location and other factors. En la construcción de algunas megatiendas, donde el edificio se cerró rápidamente después de verter la losa del piso, han ocurrido problemas de condensación durante el primer año de ocupación. Esto se relaciona con el alto nivel de humedad interior, ya que el concreto demora meses en secarse durante y después de la construcción. Concrete floors and foundations can take a long time to dry and as a result interior moisture levels can be high enough that condensation has been known to occur in climate zones 3 and 4.Building designers and architects of such buildings often include a vapor retarder in the roof assembly in order to reduce condensation risks during construction, after the building is closed up, and for up to 12 months later.What about where the vapor retarder meets the edge of the roof?Sealing and termination of vapor retarders around the perimeter is difficult. Los diseñadores de edificios deben reconocer que el objetivo de una barrera de vapor es bloquear el movimiento del aire húmedo interior en dirección al sistema de techo y permitir de forma controlada cierto nivel de permeabilidad al vapor para que la humedad que sí ingrese al sistema del techo pueda desplazarse hacia abajo y entrar al edificio. The GAF Guide to Vapor Retarder Design in Low-slope Roof Systems provides edge termination details to help guide good design.I often see dew point and vapor retarders being discussed together. Why?It's important to make sure that a vapor retarder is installed below where the dew point in the roof assembly is calculated to be. De esta manera, la barrera de vapor reducirá las probabilidades de que la humedad llegue a esa posición y forme condensación durante los períodos de frío. Calculation of the dew point takes into account the expected interior humidity levels and the possible exterior temperatures.What is condensation risk and should I always include a vapor retarder?Moisture is well known to lead to problems with respect to the durability of a building enclosure. Un diseñador profesional debe evaluar el riesgo de condensación dentro de un sistema de techo. Para este análisis, se deben tener en cuenta factores como el clima y el uso del edificio. It is important to recognize that there often is not a definitive yes/no answer to the question as to whether a vapor retarder is needed.The colder the climate, the higher the risk of condensation within the roof assembly. So, buildings located in northerly regions will generally have a higher risk of condensation forming in the building enclosure.The higher the anticipated interior moisture load, the higher the risk. Los edificios de oficinas ocupados únicamente durante el día son más propensos a tener un menor riesgo en comparación con un edificio que tiene una piscina. A building closed up during construction while a concrete slab floor is still drying will likely have a higher risk.The roof assembly design is also a factor. Los vientos intensos pueden hacer que las membranas termoplásticas single ply de fijación mecánica se hinchen y que entre aire en la estructura, lo cual puede aumentar el riesgo de condensación. Para minimizar el riesgo de condensación, los diseñadores de techos primero deben considerar adherir la membrana para techos y la capa superior de aislante, con el objetivo de dificultar el ingreso de humedad y aire interior en el sistema. If a cover board is being used, it should also be adhered.ConclusionsVapor retarders can be used to reduce the movement of vapor within a roof assembly. Se deben posicionar en el nivel más bajo posible dentro del sistema y se deben sellar todas las penetraciones. Vapor retarders in the roof assembly may be beneficial in buildings with large temperature differences from interior to exterior throughout the year, and occupancies with higher than normal interior moisture levels, either from use or during construction.Important ConsiderationsThe purpose of this article is to provide some background information and design considerations for roofing assemblies using vapor retarders. GAF fabrica y vende materiales para techos pero no es responsable del diseño y la construcción de edificios. La responsabilidad sobre el diseño corresponde al arquitecto, el ingeniero, el contratista de techado o el propietario. Esta información no se debe interpretar como exhaustiva ni se debe considerar como sustituto de las prácticas recomendadas con respecto a la aplicación. Consulta a un diseñador profesional para obtener más información.
By Authors Thomas J Taylor
01 de junio de 2021